In the automotive manufacturing industry, the painting process of automotive bumpers has a crucial impact on the product's appearance, durability, and overall quality. With the rapid development of industrial automation technology, the robotic painting line for automotive bumpers has emerged as an important force driving innovation in the automotive manufacturing industry.
The robotic painting line for automotive bumpers is usually composed of multiple functional areas organically combined. First is the pre - treatment area. Before entering the painting process, the bumpers undergo a series of pre - treatment operations in this area. Through processes such as degreasing, water washing, and phosphating, the oil, impurities, and rust on the surface of the bumpers are thoroughly removed, providing a good adhesion foundation for subsequent painting and enhancing the bonding force between the paint layer and the bumpers.
Next is the painting area, which is the core part of the entire painting line. Multiple high - precision painting robots are arranged in an orderly manner. They are equipped with advanced visual recognition systems and intelligent control systems. The robotic arms of the robots have a high degree of flexibility and precise motion control ability, capable of moving freely in three - dimensional space and accurately aiming the spray guns at various parts of the bumpers. According to the pre - set program, the robots can precisely control parameters such as the spraying angle, distance, paint flow rate, and spraying speed of the spray guns according to the shape, size, and painting process requirements of the bumpers, ensuring uniform coverage of the paint layer and avoiding problems such as missed spraying, sagging, and uneven thickness.
After painting, the bumpers enter the drying and curing area. This area is equipped with specialized drying equipment. By precisely controlling the temperature and time, the paint layer is quickly cured to form a hard, wear - resistant, and weather - resistant protective film. The drying and curing process not only determines the final performance of the paint layer but also has an important impact on the production efficiency of the entire painting line.
In addition, the painting line is equipped with a complete ventilation and exhaust gas treatment system, which is responsible for promptly discharging the paint mist and volatile organic compounds (VOCs) generated during the painting process. After a series of treatments such as filtration and adsorption, the purified gas is discharged into the atmosphere to ensure the safety and environmental friendliness of the production environment.
Bumper Loading: The automotive bumpers to be painted are accurately placed on the conveying track of the painting line manually or through automated conveying equipment. The conveying track uses a high - precision chain or belt drive system, which can smoothly and accurately convey the bumpers to each working area in sequence, ensuring the continuity and high efficiency of the entire painting process.
Pre - treatment Process: The bumpers pass through the degreasing tank in the pre - treatment area in sequence, where a special degreasing agent is used to remove the surface oil. Then they enter the water - washing tank, and the residual degreasing agent and impurities are thoroughly cleaned by high - pressure water spraying. Finally, phosphating treatment is carried out to form a phosphate conversion film on the surface of the bumpers, enhancing the surface adhesion and corrosion resistance. The bumpers that have completed the pre - treatment are automatically conveyed to the painting area.
Robotic Painting Operation: When the bumpers enter the painting area, the visual recognition system of the painting robots quickly identifies and locates them. According to the pre - set program, the robotic arms of the robots move flexibly, driving the spray guns to start the painting operation. During the painting process, the robots will adjust the parameters of the spray guns in real - time according to different parts and shapes of the bumpers. For example, for parts such as the corners and edges of the bumpers where paint accumulation or uneven thickness is likely to occur, the robots will automatically reduce the moving speed of the spray guns and increase the paint output to ensure the thickness and uniformity of the paint layer in these parts. At the same time, multiple robots cooperate with each other to achieve all - around and seamless spraying of the bumpers, greatly improving the painting efficiency and quality.
Drying and Curing: The painted bumpers are immediately conveyed to the drying and curing area. The drying equipment uses advanced heating technologies such as hot air circulation and infrared radiation, which can heat the paint layer to a suitable curing temperature in a short time and maintain it for a certain period, causing the resin and other components in the paint layer to undergo a cross - linking reaction to form a strong paint film. The temperature and time during the drying process are precisely controlled by the intelligent control system to ensure the best curing effect of the paint layer and avoid problems such as discoloration and deformation of the paint layer caused by excessive temperature or over - long time.
Bumper Unloading: After the dried and cured bumpers are cooled, they are conveyed to the unloading area through the conveying track. Here, the finished bumpers are removed from the painting line manually or by automated equipment, subjected to quality inspection and packaging, and then transported to the subsequent assembly process or the finished product warehouse.
Ultra - high Painting Quality: The precision and stability of robotic painting are far higher than those of manual painting. Robots can precisely control all parameters of the spray guns, ensuring the consistency of each painting, making the paint layer on the surface of the bumpers uniform in thickness, bright in color, and long - lasting. This high - quality painting effect not only enhances the aesthetic appearance of the bumpers but also improves their corrosion resistance and wear resistance in daily use, extending the service life of the bumpers.
Excellent Production Efficiency: The robotic painting line can operate continuously for 24 hours, and the painting speed is fast, greatly shortening the painting cycle of automotive bumpers. Compared with manual painting, the production efficiency of the robotic painting line can be increased by several times or even dozens of times, meeting the large - scale and high - efficiency production needs of automotive manufacturing enterprises and effectively reducing production costs.
Outstanding Material Utilization Rate: Robots can precisely control the amount of paint sprayed, avoiding the paint waste caused by improper operation during manual painting. By optimizing the painting path and parameters, the paint can be more accurately attached to the surface of the bumpers, reducing over - spraying and scattering, and increasing the paint utilization rate by 20% - 30%, saving a large amount of raw material costs for enterprises.
Good Working Environment and Safety: The paints and solvents used in the painting process usually contain harmful substances, which pose potential hazards to human health. The robotic painting line liberates workers from the harsh painting environment, reducing their direct contact with these harmful substances and lowering the risk of occupational diseases. At the same time, robotic operation avoids safety accidents caused by human errors, ensuring the safety and stability of the production process.
High - degree Flexible Production Capacity: The market demand for automobiles is constantly changing, and the styles and colors of automotive bumpers are also becoming more diverse. The robotic painting line for automotive bumpers has a high - degree flexible production capacity. It can quickly adapt to the painting tasks of bumpers with different models, sizes, and color requirements through simple program adjustments. This ability to quickly respond to market changes enables automotive manufacturing enterprises to gain an advantage in the fierce market competition.
Many well - known automotive manufacturing enterprises, such as Toyota, Volkswagen, and General Motors, have widely adopted the robotic painting line for automotive bumpers. Taking an automotive manufacturing enterprise as an example, before introducing the robotic painting line, the painting process of its automotive bumpers mainly relied on manual operation, with low production efficiency and a defective product rate of up to about 10%. After introducing the robotic painting line, the production efficiency increased by more than 50%, the defective product rate decreased to less than 3%, and millions of yuan in paint costs were saved every year.
The widespread application of the robotic painting line for automotive bumpers has promoted the development of the entire automotive manufacturing industry towards intelligence and automation. It not only improves the quality and production efficiency of automotive products and reduces production costs but also provides a more environmentally friendly and safe production method for automotive manufacturing enterprises, promoting the sustainable development of the automotive industry. With the continuous progress and innovation of technology, the robotic painting line for automotive bumpers will play an even more important role in the future automotive manufacturing field, leading the industry to a higher - level development stage.
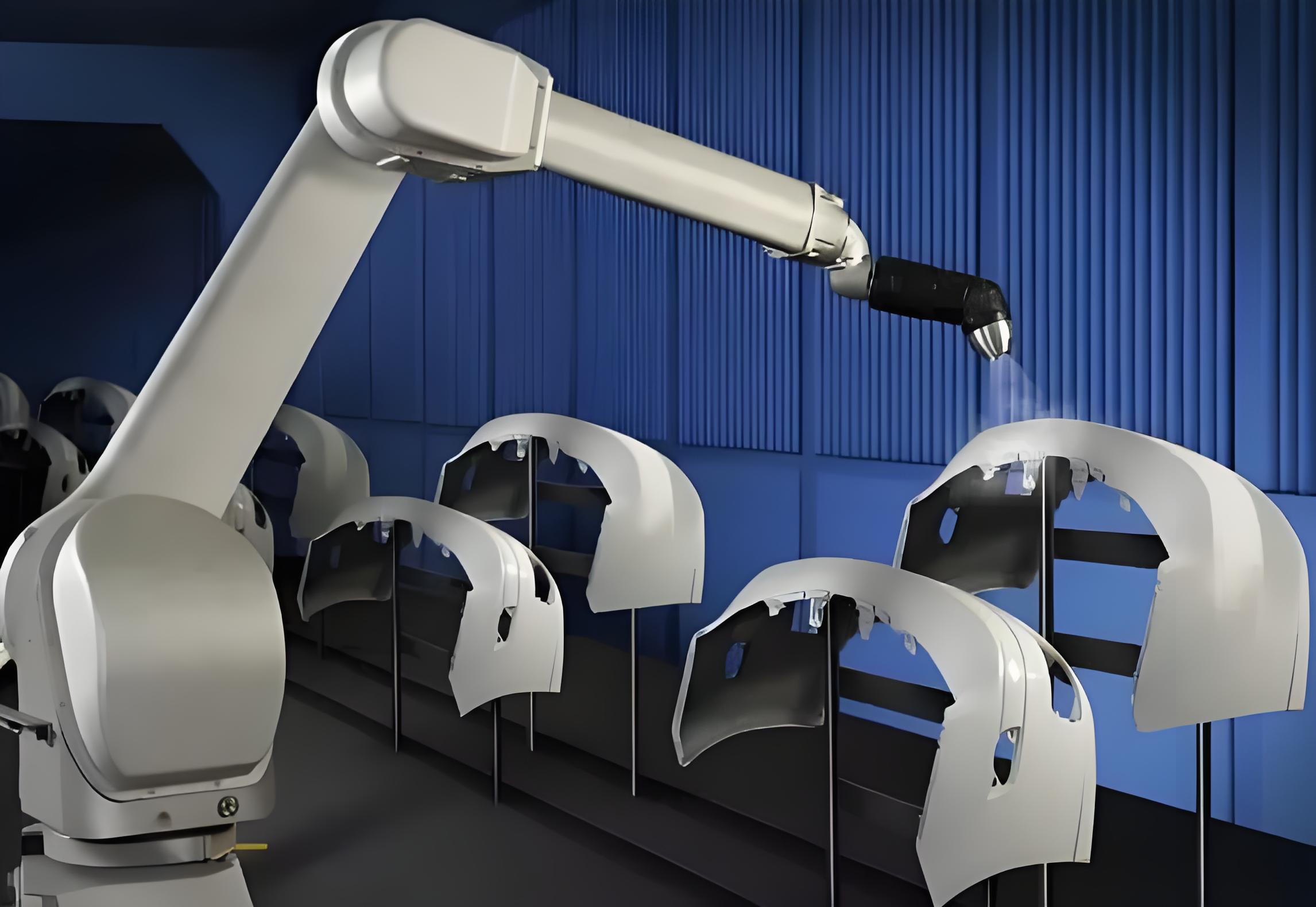